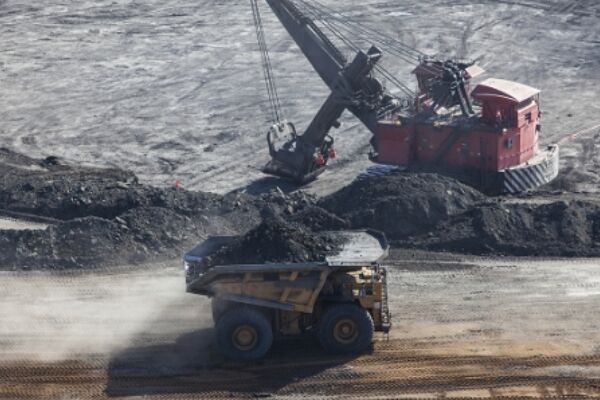
Le rôle crucial d’une lubrification haute performa...
Les conditions extrêmes dans le secteur minier provoquent de l’usure et des arrêts machines. Eurol propose des solutions pour améliorer la durée de vie et l’efficacité des ...
9 mai 2023
Tout le monde sait qu’en plus de l’huile, un moteur a également besoin de liquide de refroidissement. Autrefois, on pouvait se fier à la couleur pour choisir le bon produit, mais ce temps est révolu. À quoi sert exactement un liquide de refroidissement, quelles sont les différences entre les technologies, et quelles sont leurs propriétés ? Pourquoi n’est-il plus possible de faire un choix simplement en se basant sur la couleur ? Dans cet article, nous vous proposons d’explorer plus en détail l’univers des liquides de refroidissement automobiles.
Commençons par la fonction de base : un liquide de refroidissement, comme son nom l’indique, doit avoir un effet réfrigérant. Dans une situation idéale, toute l’énergie issue de la combustion du carburant serait utilisée pour le mouvement. En réalité, la majeure partie de cette énergie est convertie en chaleur. Même les véhicules électriques et hybrides avec de grandes batteries dégagent beaucoup de chaleur pendant la conduite (décharge) et la recharge. Ces systèmes cessent de fonctionner en cas de surchauffe, c’est pourquoi un système de refroidissement est indispensable.
En plus d’évacuer la chaleur, les liquides de refroidissement ont d’autres fonctions :
• Protéger contre le gel
• Élever le point d’ébullition au-dessus de la température de fonctionnement
• Protéger les métaux du système de refroidissement contre la corrosion
• Limiter la formation de mousse
La fonction principale du liquide est, comme mentionné, de transporter l’excès de chaleur vers le radiateur, où elle est dissipée dans l’air extérieur. L’eau est très efficace pour absorber et transférer la chaleur, mais elle présente deux inconvénients majeurs : elle gèle à 0°C et bout à 100°C. De plus, les minéraux et sels présents dans l’eau (y compris l’eau potable) peuvent avoir des effets négatifs sur les matériaux du système de refroidissement.
Pour éviter ces effets indésirables, on utilise des glycols comme base des liquides de refroidissement, le plus souvent le monoéthylène glycol (MEG). Le monopropylène glycol (MPG) est également utilisé, mais sa capacité à transférer la chaleur est généralement insuffisante pour les moteurs à combustion. Étant moins toxique, le MPG est plutôt utilisé dans l’industrie alimentaire. Une troisième option est le liquide de refroidissement à base de glycérol, également connu sous la spécification G13. Bien que le glycérol soit plus respectueux de l’environnement que le MEG, il est moins utilisé dans ce domaine car il sert également de matière première dans les cosmétiques. Le glycérol est un sous-produit de la production de biocarburants ou provient de matières végétales.
Un liquide de refroidissement composé de plusieurs éléments, car – en plus du monoéthylène glycol (MEG) – des additifs sont nécessaires pour conférer au liquide les propriétés souhaitées (nous y reviendrons plus loin). L’association MEG + additifs est appelée « antigel » ou « concentré ». L’antigel doit être dilué avec de l’eau déminéralisée ou adoucie avant de pouvoir être utilisé dans un système de refroidissement.
Dans l’eau déminéralisée, les minéraux tels que le calcium et les sels sont éliminés. Le calcaire empêche le transfert de chaleur et les sels peuvent corroder les métaux du système.
Ce n’est qu’après dilution de l’antigel que l’on obtient un liquide de refroidissement prêt à l’emploi, aussi appelé « Ready-Mix » ou « coolant ». La quantité d’eau déminéralisée utilisée pour diluer le concentré détermine la plage de température du mélange. En règle générale, un mélange 50/50 assure une protection jusqu’à -36°C, tandis qu’un rapport 40/60 (40% de concentré et 60% d’eau déminéralisée) offre une protection jusqu’à -26°C. Une concentration plus élevée d’antigel n’élargit pas la plage de température ni ne l’améliore. À l’inverse, une concentration trop faible fait perdre au mélange ses propriétés de protection contre la corrosion. Voir le graphique ci-dessous pour plus de détails :
Pour conférer au liquide de refroidissement ses propriétés spécifiques, des additifs chimiques sont nécessaires. Ces additifs sont ajoutés afin de prévenir, entre autres, la corrosion, la cavitation (formation et destruction de bulles d’air pouvant endommager la pompe à eau), les dépôts et les boues (sédiments de matières insolubles).
Afin de prévenir les intoxications dues à l’ingestion du liquide de refroidissement, un agent amérisant est systématiquement ajouté. Cela garantit que, en cas de fuite inattendue, les chiens ne boivent pas le liquide. Cela empêche également les enfants de le consommer. En cas d’ingestion, humains et animaux peuvent tomber gravement malades.
On peut donner au liquide de refroidissement n’importe quelle couleur à l’aide d’un colorant. Cela signifie qu’il n’est plus possible aujourd’hui de « se fier » à la couleur du liquide ou à ses habitudes. Autrement dit, la couleur ne dit rien de la qualité ni du type de liquide.
On y trouve également des stabilisants contre les précipitations (dépôts de silicates), des dispersants pour garantir la tolérance à l’eau dure, un tampon de pH pour maintenir le niveau d’acidité, ainsi que des agents anti-mousse pour éviter que l’air ne soit emprisonné dans le liquide pendant la circulation.
La technologie IAT est aussi connue sous le nom de liquide « conventionnel » ou « ancien ». Elle a un intervalle de remplacement court (tous les 2 ans) et est souvent de couleur verte ou bleue.
Pour répondre aux exigences de protection, ce liquide contient des inhibiteurs inorganiques (minéraux) tels que silicates, nitrates, amines, phosphates et/ou borates. Il fonctionne en créant une fine « couche de protection » sur les métaux, qui agit comme un bouclier. Cependant, ces inhibiteurs minéraux s’usent avec le temps, ce qui signifie que cette couche protectrice ne peut plus se régénérer après un certain temps, rendant le système plus vulnérable.
L’avantage de ce liquide est qu’il agit rapidement, mais son effet chimique s’estompe également rapidement. La couche formée agit aussi comme un isolant thermique, ce qui limite légèrement le transfert de chaleur.
Un liquide de refroidissement OAT est à base de glycol (MEG ou MPG) et contient des inhibiteurs organiques, appelés carboxylates. Il ne contient aucun inhibiteur minéral. Ces inhibiteurs organiques sont sélectifs : au lieu de former une couche protectrice sur tout le système, ils agissent uniquement aux endroits où la corrosion commence à apparaître.
La consommation d’additifs est donc bien plus faible qu’avec un IAT, ce qui permet un intervalle de remplacement bien plus long (long-life).
L’inconvénient est que la protection est réactive, c’est-à-dire qu’elle ne s’active qu’une fois que la corrosion commence à apparaître, ce qui entraîne un léger retard dans l’action protectrice.
Pour certains métaux légers, cette forme de corrosion localisée (propre aux OAT) n’est pas acceptable. C’est pourquoi un liquide hybride a été développé, combinant les inhibiteurs minéraux du IAT et les inhibiteurs organiques du OAT. Il s’agit d’un liquide OAT enrichi en petites quantités de silicates, borates, molybdates ou nitrates selon l’application. Ce liquide combine la longévité du OAT avec la protection rapide du IAT.
Les Lobrids représentent la dernière génération de liquides de refroidissement, dans lesquels l’effet hybride d’un HOAT est encore mieux adapté et ajusté à l’application. Le niveau d’inhibiteurs minéraux y est réduit, et une plus grande proportion d’inhibiteurs organiques est utilisée. Le nom « Lobrid » vient de la combinaison des termes low et hybrid. Les inhibiteurs minéraux utilisés sont souvent mentionnés dans le nom, par exemple : Si-OAT et P-OAT (respectivement à base de silicates ou de phosphates), ou une combinaison des deux : PSi-OAT.
La gestion thermique dans un véhicule électrique à batterie (BEV) est essentielle, que ce soit pour maintenir la température des batteries, du moteur ou des composants électriques haute puissance. On distingue deux types de systèmes de refroidissement :
• Refroidissement conventionnel du pack batterie
• Batteries immergées dans un liquide (pack batterie immergé)
Les batteries perdent en capacité lorsqu’elles deviennent trop chaudes. Elles perdent également en capacité lorsqu’elles sont trop froides. À basse température, elles ne peuvent même pas se recharger. Actuellement, le système dominant est un refroidissement externe du pack batterie à l’aide de liquides de refroidissement classiques à base de MEG. Parmi les véhicules concernés : Tesla Model S, Audi eTron, Mercedes-Benz EQC et BMW i3.
La technologie de recharge rapide est un point central dans le développement des véhicules. Elle génère potentiellement des températures très élevées. Il existe déjà des véhicules capables de charger à une vitesse équivalente à 960km/h. Des vitesses supérieures à 1400km/h sont même annoncées prochainement. Ces vitesses ne peuvent être atteintes qu’avec des packs batterie immergés, capables de gérer efficacement la température. Les fluides utilisés s’apparentent à des fluides pour transformateurs mais avec une viscosité bien plus faible. On les appelle aussi « fluides thermiques » ou « fluides diélectriques ».
Les fluides thermiques ont des exigences différentes des liquides de refroidissement pour moteurs à combustion. Ils doivent avoir un point d’éclair élevé, être ignifuges et non conducteurs.
Maintenant que nous avons exploré les différentes technologies et leur évolution, une question revient souvent : « pourquoi existe-t-il autant de types de liquides de refroidissement ? » En théorie, la solution idéale serait d’utiliser un liquide long-life offrant une protection maximale pour tous les systèmes de refroidissement. Mais en pratique, cela n’est pas possible. Chaque constructeur (OEM) a sa propre vision de son moteur et des matériaux utilisés. Les exigences fixées par les constructeurs sont définies dans des spécifications, auxquelles un liquide de refroidissement approuvé doit répondre selon l’une des technologies décrites. C’est pourquoi il est essentiel de consulter toujours le Conseiller en huile Eurol. Cet outil vous aidera à faire le bon choix du fluide ou du liquide de refroidissement adapté à votre application.
Pour toute question complémentaire, n’hésitez pas à nous contacter - nos spécialistes se feront un plaisir de vous aider.
Les conditions extrêmes dans le secteur minier provoquent de l’usure et des arrêts machines. Eurol propose des solutions pour améliorer la durée de vie et l’efficacité des ...
Nous présentons le Eurol Coolant -36°C G12 EVO. Il s'agit d'un liquide de refroidissement de dernière génération développé à partir de la technologie LOBRID PSi-OAT, spécia...
Économies de carburant, passages de vitesses plus fluides, durée de vie prolongée et carters plus compacts : ce sont les principaux moteurs de l’innovation dans le domaine ...
De nombreux véhicules diesel modernes utilisent l’AdBlue pour répondre aux normes d’émission. Mais qu’est-ce que l’AdBlue et comment fonctionne-t-il ? Dans cet article, nou...
Les conditions extrêmes dans le secteur minier provoquent de l’usure et des arrêts machines. Eurol propose des solutions pour améliorer la durée de vie et l’efficacité des ...
Nous présentons le Eurol Coolant -36°C G12 EVO. Il s'agit d'un liquide de refroidissement de dernière génération développé à partir de la technologie LOBRID PSi-OAT, spécia...
Économies de carburant, passages de vitesses plus fluides, durée de vie prolongée et carters plus compacts : ce sont les principaux moteurs de l’innovation dans le domaine ...
De nombreux véhicules diesel modernes utilisent l’AdBlue pour répondre aux normes d’émission. Mais qu’est-ce que l’AdBlue et comment fonctionne-t-il ? Dans cet article, nou...