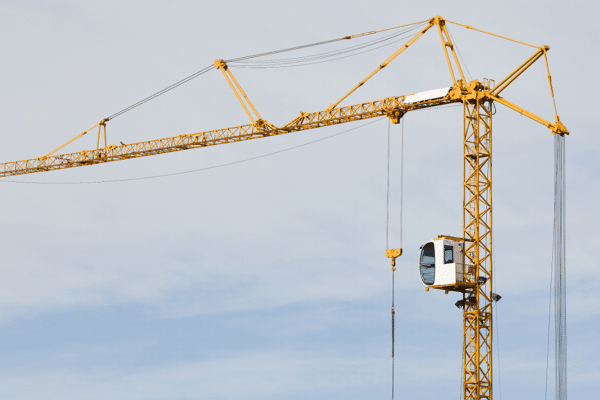
Protection contre la corrosion des câbles pendants
Une entreprise de grues a été confrontée à une corrosion sévère sur les câbles de flèche de ses grues à tour mobiles, ce qui a entraîné des coûts de maintenance élevés et d...
13 novembre 2023
Earthmoving equipment such as excavators, bulldozers, wheel loaders, shovels, tractors, crawler machines, and dump trucks are often exposed to heavy loads. This has a significant impact on the lubrication points, especially the pin-and-bush connections. Sand and water pose considerable challenges for the lubrication of these heavily loaded pin-and-bush connections. Sand acts as an abrasive, increasing wear, while water can reduce the lubricating properties of the grease and cause rust formation.
It is important to perform regular maintenance, including cleaning and re-lubricating the pin-and-bush connections. Special attention must be paid to the choice of grease, which should have water-repellent properties to prevent the impact of moisture on lubrication.
It is common to use Multi EP2, molybdenum disulfide, or PTFE greases for lubricating pin-and-bush connections. However, these traditional greases were designed decades ago for applications and machines of that time. In many cases, these greases simply no longer meet the requirements for lubricating modern equipment. This leads to insufficient lubrication, which in turn can lead to wear, downtime, and high maintenance costs.
Selecting the right grease, taking into account the challenges of sand, water, and heavy loads, is an important step in improving the maintenance process and preventing unexpected downtime. In addition, operators and maintenance staff should be aware of the limitations of standard greases. There should be a willingness to explore the possibilities of more advanced new generation greases.
Modern technological developments in synthetic base oils, thickeners, and additives have led to new advanced greases that perform better under extreme conditions. These modern anti-wear additives provide a protective layer that prevents wear and corrosion and extends the lifespan of the connection. This prevents unexpected downtime and high maintenance costs.
The water-resistant Eurol Grease CS-2 / 502-S is a good example of a modern grease. This grease contains the Eurol SYNGIS Technology, which provides unmatched anti-wear and anti-corrosion properties. This prevents unexpected downtime and greatly reduces maintenance costs. Biodegradable versions are also available.
Une entreprise de grues a été confrontée à une corrosion sévère sur les câbles de flèche de ses grues à tour mobiles, ce qui a entraîné des coûts de maintenance élevés et d...
We introduce the Fultrax 75W-90 LS, a fully synthetic transmission oil with limited slip properties.
Les codes couleur des lubrifiants sont une composante essentielle du maintien d’un environnement de travail industriel sûr et efficace. Lisez-en plus dans cet article du ce...
La réduction de l’empreinte CO2 des processus industriels devient un enjeu de plus en plus important. Dans ce contexte, les économies d’énergie jouent un rôle crucial.
Une entreprise de grues a été confrontée à une corrosion sévère sur les câbles de flèche de ses grues à tour mobiles, ce qui a entraîné des coûts de maintenance élevés et d...
We introduce the Fultrax 75W-90 LS, a fully synthetic transmission oil with limited slip properties.
Les codes couleur des lubrifiants sont une composante essentielle du maintien d’un environnement de travail industriel sûr et efficace. Lisez-en plus dans cet article du ce...
La réduction de l’empreinte CO2 des processus industriels devient un enjeu de plus en plus important. Dans ce contexte, les économies d’énergie jouent un rôle crucial.